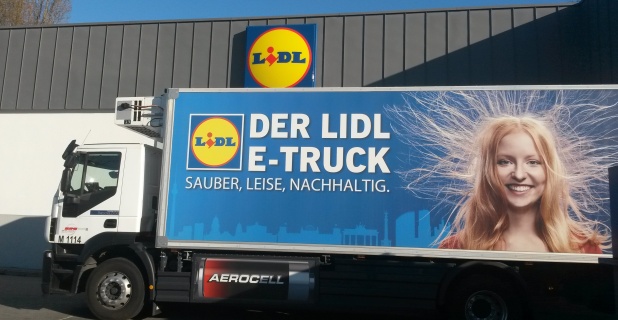
Sustainability and climate protection are subjects that ultimately also pertain to logistics. Recently, GS1 Germany presented the Lean and Green Award to four companies who plan to reduce their logistics-related CO2 emissions by 20 percent within five years. Award winner Lidl Stiftung emphasizes optimized route planning, the reduction of empty runs or avoidance of smaller subsequent deliveries. In this interview with iXtenso, the company explains the different measures.
Lidl is one of four companies that won the Lean and Green Award by the GS1 Germany for its sustainability action plan. What are the provisions of this plan?
Lidl: With the “On the way to a better tomorrow“motto, Lidl accepts responsibility and emphasizes sustainability against the backdrop of climate change, increasing resource scarcity and rising energy prices. With this in mind, we continuously work on solutions to protect the climate and the environment within our means.
We revised our logistics concept and created an action plan to reduce CO2 by 20 percent within the entire logistics area we are responsible for. Based on a so-called “measured baseline“, Lidl first determined its current state. This pertained to the fields of procurement logistics (including the import division), construction (logistics real estate), cost management (electricity, gas, fuel oil) and distribution (store supply). Our action affects the entire supply chain with custom-fit measures.
How realistic is it to achieve these goals? And how is this development being measured?
Lidl: For many years, Lidl has focused on efficient logistics. Today all transportation activities are already centrally controlled to ensure an optimal level of utilized capacity of carriers. However, this area still offers more potential cost savings. By using targeted measures such as optimizing route planning or converting to alternative carriers, we will emphatically work on implementing our goals for all the defined areas. Within the scope of the “Lean and Green“ initiative by the GS1, the German Technical Inspection Association (TÜV) inspects the overall plan. In addition, Lidl regularly reports to GS1 on intermediate results for implementing the action plan.
What efforts does it take for such a large company to implement this concept? What are the biggest challenges and what is easiest to implement?
Lidl: As a grocery retailer, we work on lean logistical processes every day and are very well positioned in the respective divisions that pertain to logistics, costs and distribution. One of the biggest challenges is in developing further potential for optimization.
However, over the past few years, Lidl has shown numerous times that its efforts in developing sustainable and resource conservation measures, among others in the logistics area, have paid off. In 2006, we set up our warehousing and logistics by implementing various energy conservation measures. In this instance, we use generated waste heat for the refrigeration and air conditioning of temperature-sensitive foods and for heating the storage areas.
We exclusively use cooling systems operated with natural cooling agents with every new development. We are able to direct our actions towards these time-tested standards in the future.
From your point of view, what significance do the sustainability efforts by Lidl have for consumers/customers? And how is this commitment to sustainability being received?
Lidl: Lidl is aware of its responsibility for man and nature and continuously lobbies to improve in the areas of environment and climate protection, employees, corporate citizenship and selection of goods. Climate protection is one of the biggest challenges of our times.
By revising and optimizing our logistics concepts, we primarily want to do justice to our corporate social responsibility. Being part of society, our customers naturally also benefit from this.
Are there other areas beyond logistics where Lidl uses sustainable solutions?
Lidl: We would like to update you on further areas in which we also follow a sustainability approach:
- Product selection: We know that today our customers increasingly value products that represent a sustainable way of life and therefore conscious consumption. This is why we have been offering an attractive selection of various products from sustainable agriculture and fair trade for many years. These items are fair trade-certified and carry the organic label.
- Cooperation: Still further potential savings can be achieved by a collaboration between manufacturers and Lidl, for instance by reducing the packaging size. In this case, Lidl already focuses on working with selected suppliers.
- Retail store construction: Lidl sets high sustainability standards with its real estate. The new generation of retail stores therefore features climate-friendly technologies that were developed by Lidl during an extensive process. Our expectation was to combine more sustainable building technology and energy-efficient construction with attractive architecture. At this point, Lidl has already built over 200 retail stores in this way.
- Warehouse construction: In our central distribution centers, we use the generated waste heat for the refrigeration and air conditioning of temperature-sensitive foods and for heating the storage areas for example. We exclusively use cooling systems operated with natural cooling agents with every new development. In addition, we reduce heat loss by using energy efficient insulation materials.
When is it beneficial for retailers to pursue sustainable concepts?
Lidl: As a commercial enterprise, we assume responsibility for the environment and nature within the scope of our possibilities. In our daily actions, we accept economic, social and ecological responsibility to be able to reliably supply our customers of tomorrow and offer our employees a safe workplace in the future.
Interview by Natascha Mörs; iXtenso.com